急拡大するEVや5G向け電子基板の全数検査を可能とする 世界最速の3D X線検査装置「VT-X750-V3」を発売
オムロン株式会社(本社: 京都市下京区、代表取締役社長CEO: 山田義仁)は、世界最速*¹で電子基板を3D検査できるCT型X線自動検査装置*² 「VT-X750-V3」を11月20日からグローバルで発売します。5GやEV、自動運転のニーズが高まる中で、生産性を維持向上しつつ顧客製品の品質を担保するために、電子基板を全数検査し、安心・安全な社会づくりに貢献します。
【世界最速の検査スピードを実現したCT型X線自動検査装置「VT-X750-V3」】
近年、5GやEV、自動運転などで使用される電子基板の需要が急増しています。特に車載をはじめとするこれらの用途は、人命に関わることから、品質要求は一層高まっています。また、最終製品の性能向上や安全性を担保するため、基板上に搭載部品数を増やせるよう、基板の両面への部品実装や部品を集約したICチップ化が進んでいます。外観では検査できないこれらの部品をより正確に検査するには、従来のX線による2D撮像ではなく、3Dでの検査が必須です。しかし、3D検査は撮像と画像処理に時間がかかるため、運用効率と高品質な検査の両立が非常に困難なことが課題でした。製造現場では、2D検査時と同等の生産数を確保するために、生産品の全数ではなく一部のみの検査、または、全数検査を行うために、生産工程から離れた場所に置いた検査工程で、時間をかけて対応する場合もあることが現状でした。
【同じはんだを2DでX線撮像した画像(左)と、3DでX線撮像した画像(右)】
今回、発売する 「VT-X750-V3」は、現行モデルより検査速度を1.5倍に高速化することでで、複雑な基板でも全数検査を可能としました。搭載するオムロン製制御機器をシームレスに制御することで実現した独自の連続撮像技術*³と、従来比2倍*⁴の感度を持つカメラの採用により、クリアな3D画像の高速撮像を実現しました。これにより、高性能な検査を短時間で行うことができます。また、AIによって検査の撮影条件設定を自動化させ、基板検査プログラムの作成時間を大幅に短縮させます。オムロンは、これらの技術革新に加え、30年以上にわたり検査の現場で培ったノウハウを活かして、お客様の生産性との両立に貢献します。
【複雑な基板・部品の検査事例】
オムロンは、3つの" i "、「integrated(制御進化)」、「intelligent(知能化)」、「interactive(人と機械の新しい協調)」からなる戦略コンセプト「i-Automation!」のもと、製造業のモノづくり現場革新に取り組んでいます。豊富な制御機器のすり合わせとはんだ検査の知見を結集することで、i-Automation!を体現する「VT-X750-V3」で実装工程全体の不良低減から、不良を発生させない生産ラインの構築に向けたトータルソリューションを提案していきます。
*¹ 世界最速:基板検査業界におけるフル3D-CT型X線自動検査装置として、世界最速。2021年10月当社調べ。
*² CT型X線自動検査装置:X線を用いて、ヒトの目に見えない構造物内部の連続的な断面の画像を撮影し、コンピューター処理することで、3次元の立体的な画像を得る技術を搭載した検査装置。医療機関などで利用されているCTスキャンと同様の技術が使われている。
*³ 連続撮像技術:立体画像を移動しながら止めることなく撮像する技術
*⁴ 従来比2倍:旧モデルに比べて、約2倍の感度。同一撮像条件で、イメージセンサ(撮像素子)がX線を光として感じる度合い。
主な特長
従来比1.5倍の検査速度をオムロン独自の連続撮像技術により実現
従来の高画質な3D-CTデータ(3D画像)の撮影はそのままに、撮影のためのハードウェア制御を高度最適化することで、従来比1.5倍の高速撮像を実現しました。これにより、従来同等の生産性で、高精度な全数検査が可能となります。
ハードウェア制御の高度最適化においては、オムロンの制御機器で培ったノウハウを集結し、高速でシームレスな連続撮影を実現するとともに、フィードバック制御による、より正確な位置での撮影を実現しました。これらの独自技術により、クリアな3D-CT画像(3D画像)の撮像が実現できました。さらに、3D-CTデータ(3D画像)の生成にあたっては、自社開発による最新の3D-CTアルゴリズムの搭載と高感度高速カメラの採用により、よりノイズのすくない3D画像が生成できるようになりました。
【従来製品との検査速度の比較】
パワーデバイスの検査
IGBTやMOSFET*⁶などのパワーデバイスに最適化した検査ロジックを新たに追加しました。また、基板実装後のアセンブリ工程でのスルーホールコネクタのはんだ充填検査や、近年採用が増加しているSiP/PoPパッケージ*⁷やプレスフィットコネクタなどの検査にも多くの採用実績があります。
特に、パワーデバイスにおいては、パワー半導体がSiからSiCやGaN*8へ変化しつつある中、放熱の課題はますます重要となってきます。EVの課題である1回の充電における走行距離の延長や、高出力化、小型・軽量化に対して、放熱の課題は避けては通れません。オムロンではそれに先駆けて、放熱の課題の一つであるはんだ接合中のボイド検査について、独自の検査アルゴリズムを開発し、搭載しました。
【GaNパワーデバイス(左)とSiP(右)の3D-CT撮像事例】
AIによるスキルレス化、自動化
検査対象物や、部品、また裏面に搭載された部品の影響などにより、X線撮像条件の最適化が必要です。それらの撮像条件の設定には、いくつかのパラメーターがあり、従来は、カット&トライを繰り返しながら、最適な撮像条件を設定していました。それらの設定を、AIにより自動で設定することができるようになりました。これにより、撮像条件の設定が大幅に短縮できました。
また、VT-X750-V3で撮像した3D-CTデータ(3D画像)を用いた検査には、3D画像処理の技術が必要となります。その3D画像処理の設定を事前に登録しておくことで、生産現場では自動で検査を行っています。
しかしながら、その3D画像処理の設定には、専門スキルが必要となっていました。この度、その一部を自動化することで、専門スキルに頼ることなく、設定時間を短縮することができました。
被ばくリスクの低減
作業者への被ばく防止はさることながら、検査するワーク上の半導体部品などの被ばくによる故障リスクの低減が大きな課題です。今回、基板の表・裏や、搭載される位置などによって、部品ごとの被ばく量をより正確にシミュレーションできる機能を追加しました。
これにより、部品ごとの被ばく量の限界値と照らし合わせることで、被ばくによる部品故障のリスクを低減することができます。
【部品ごとの被ばくシミュレーション】
*⁵ Mサイズ基板の全面検査の時間。基板の搬入・搬出時間は除く。2,000~3,000ピンのBGA2個やSiPを含む、 基板の表面、裏面の全部品の3D検査にかかる時間。
*⁶ IGBTやMOSFET:パワーデバイスは、バッテリーに蓄えられた電気を使って、モータなどを駆動させるために必要な部品で、バッテリーなどの直流の電気を、モータ駆動に必要な交流に変換する部品。特に、近年では、自動車や鉄道などの電動化では重要な部品の一つとなっている。家庭用の家電製品では、コンセントからの交流の電気をそのままモータなどの駆動に使えるが、電気自動車やPHEVでは、バッテリーを駆動源としており、直流から交流に変換することが必要。IGBTやMOSFETはパワーデバイスの代表的な一種で、用途によって採用が異なる。
*⁷ SiP/PoPパッケージ:SiP=System in Package、PoP=Package on Packageの略。いずれも基板に実装される部品の名称で、従来のIC/LSI部品の内部構造は単層であったが、SiPやPoPなどの内部構造は、複数層となっており、複雑な構造となっている。複雑な構造となることで、X線検査としてはより3Dでの検査が必要となっている。なお、SiPはコネクテッドカーやスマートフォン端末などの5G通信用部品として用いられることが多く、PoPはスマートフォンのアプリケーションプロセッサ(メインのCPU)として用いられることが多い。*⁸ SiCやGaN:従来の半導体素子は、パワーデバイス向けも含めてSi(シリコン/ケイ素)が主流であるが、パワーデバイス向けでは電気容量の大容量化や高圧/高電流化に向けて耐熱温度が課題となっている。SiC(シリコンカーバイド/炭化ケイ素)やGaN(ガリウムナイトライド/窒化ガリウム)は、Siよりも耐熱性に優れ、次世代のパワー半導体素子として期待されている。
展示会への出展について
2022年1月19日~21日に東京ビッグサイトで開催される「インターネプコン ジャパン 2022」のオムロンブースにて「VT-X750-V3」を紹介します。基板と部品のX線自動検査のデモンストレーションをご覧いただけます。
展示会:インターネプコン ジャパン 2022
開催日時:2022年1月19日(水)~21日(金)
開催場所:東京ビッグサイト
ブースNo:東3ホール
< “i-Automation!”について>
オムロンは、製造業のモノづくり現場を革新するコンセプトを"i-Automation!"のもと、次の3つの"i"からなる オートメーションの進化によって製造現場の生産性を飛躍的に高め、付加価値の高いモノづくりの実現を目指しています。「integrated(制御進化)」は、これまで熟練工に頼っていた匠の技を、誰もが簡単に実現できるよう、オートメーション技術を進化させます。「intelligent(知能化)」は、幅広い制御機器とAIを活用し、機械が自ら学習して状態を保全するなど、進化し続ける装置や生産ラインを実現します。「interactive(人と機械の新しい協調)」は、同じワークスペースで人と機械が共に働き、機械が人の動きや考えを理解しアシストするなど、生産現場を知り尽くす制御機器メーカーのオムロンならではの、人と機械の新しい協調関係を提供します。
<オムロン株式会社について>
オムロン株式会社は、独自の「センシング&コントロール+Think」技術を中核としたオートメーションのリーディングカンパニーとして、制御機器、電子部品、社会システム、ヘルスケア、環境など多岐にわたる事業を展開しています。1933年に創業したオムロンは、いまでは全世界で約30,000名の社員を擁し、約120の国と地域で商品・サービスを提供しています。詳細については、https://www.omron.co.jp/ をご参照ください。
本プレスリリースは発表元が入力した原稿をそのまま掲載しております。また、プレスリリースへのお問い合わせは発表元に直接お願いいたします。
このプレスリリースには、報道機関向けの情報があります。
プレス会員登録を行うと、広報担当者の連絡先や、イベント・記者会見の情報など、報道機関だけに公開する情報が閲覧できるようになります。
このプレスリリースを配信した企業・団体
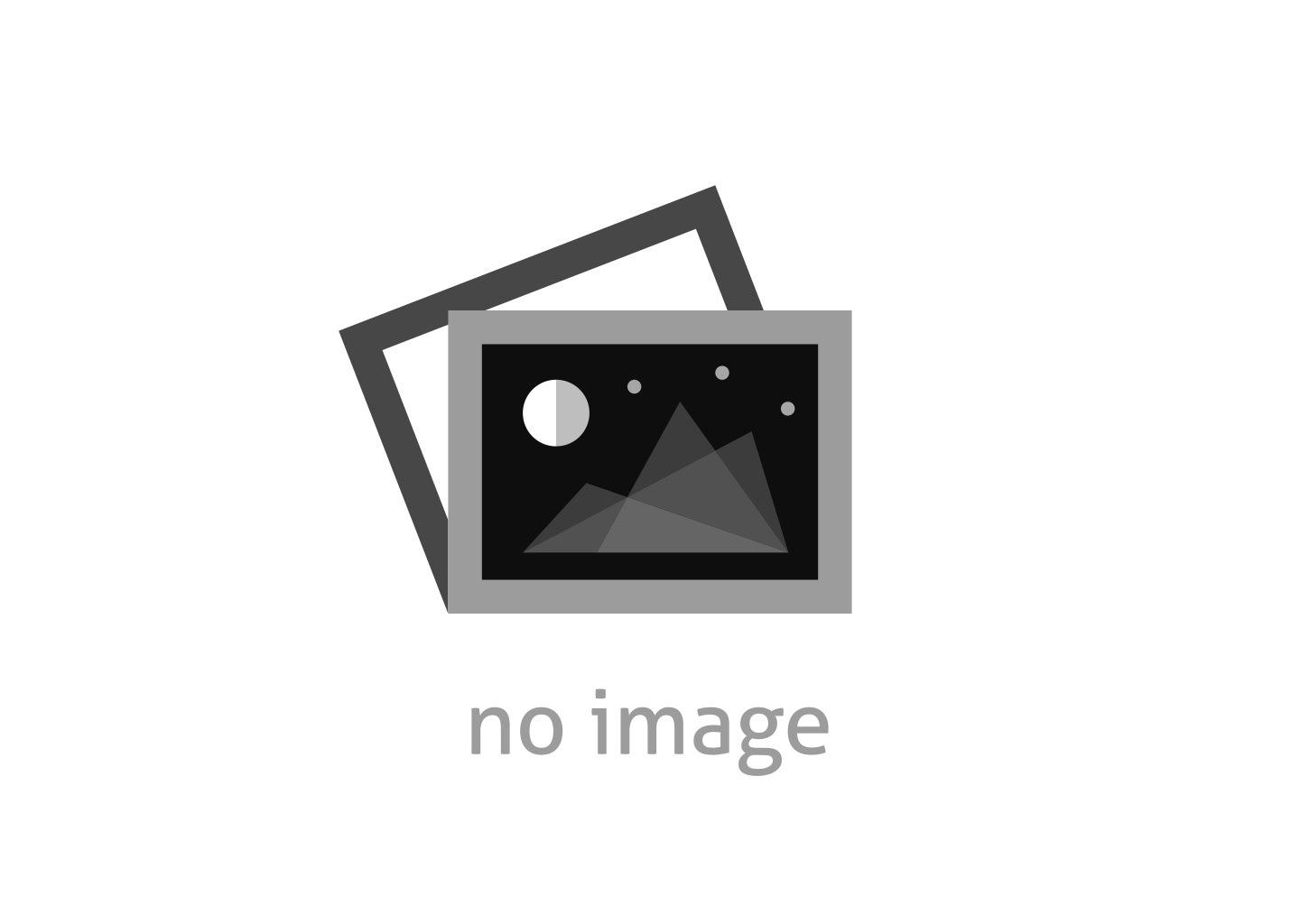
- 名称 オムロン株式会社
- 所在地 京都府
- 業種 電気機器
- URL http://www.omron.co.jp/
過去に配信したプレスリリース
情報制御と安全制御を進化させたコントローラー「NX502」を新発売
2023/4/17
オムロン、「KYOTOGRAPHIE 京都国際写真祭2023」に協賛
2023/4/13
ユビ電株式会社への出資について
2023/4/7
電子部品事業、「カーボンニュートラル」特設サイトオープン
2023/3/28